ratter
New member
Skip ahead to the money shots...
A fellow RT'er is having an ampfest this weekend. I wanted to put together something to bring along. Can we build a guitar in a week or so? A guitar that doesn't completely suck? I think that remains to be seen. But I'm going to cheat a bit, so maybe.
The first thing to do is pick appropriate birthin' music and away we go.
Like any good build, it starts with a delivery from the lovely Pacific Northwest.
Next up, opening the box!!
A fellow RT'er is having an ampfest this weekend. I wanted to put together something to bring along. Can we build a guitar in a week or so? A guitar that doesn't completely suck? I think that remains to be seen. But I'm going to cheat a bit, so maybe.
The first thing to do is pick appropriate birthin' music and away we go.
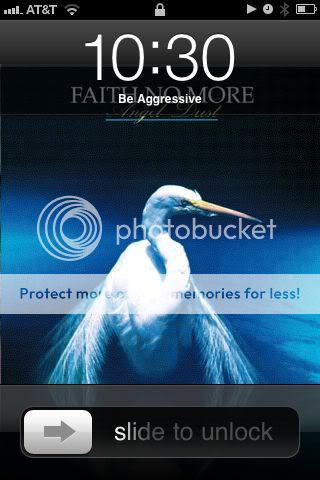
Like any good build, it starts with a delivery from the lovely Pacific Northwest.
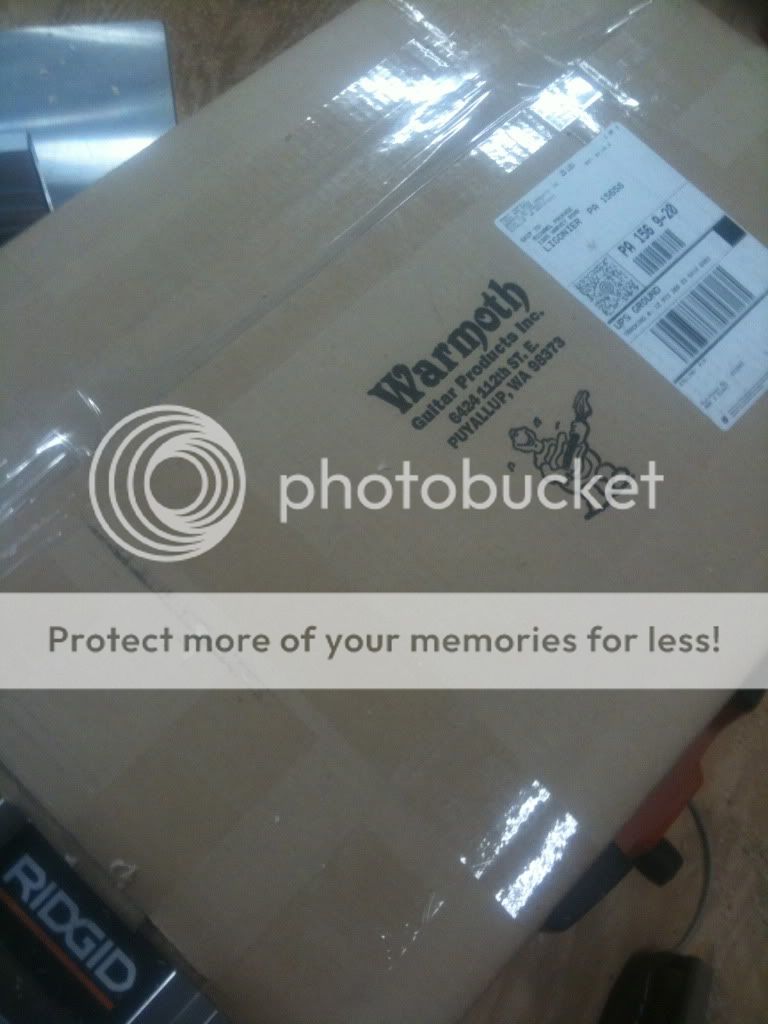
Next up, opening the box!!